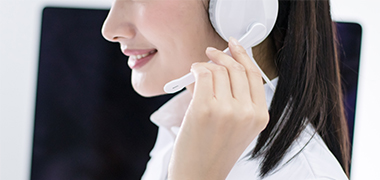
- Contact:Minister Xu
- Mobile:13841408476
- Tel:024-44837288
- Fax:024-44837004
- E-mail:xuming58@126.com
- Web:m.wanderlustamericana.com
- Address:No.110 XiangHuai Road
Benxi Economic Development Zone
Liaoning Province
Polygon Offers Double Insulation Dielectric Composite Tubing for Electric Motors
04 Dec,2020
Polygon Company highlights its Double Insulation Dielectric Composite Tubing for electric motor applications. Polygon Tube double insulation tubing is customizable to an individual application’s needs, thus ensuring the highest possible quality and greatest safety benefit in each individual motor design.
Used as a sleeve within the armatures of electric motors, Polygon Tube double insulation tubing acts as a secondary layer of insulation and provides shock protection to the operators of electrical tools and appliances. The use of the additional layer of insulation allows the appliance to be rated "Double Insulated" and the need for grounding of the unit is eliminated.
Polygon’s design and performance engineers use their extensive knowledge and experience in composites science to assist customers in determining the best fiber architecture and finishing to produce ideal secondary insulating sleeves for every application. This includes customizing sizes and machining holes and cutouts to fit numerous applications.
Composite materials are the ideal choice for insulative applications because they can be tailored to almost any engineering challenge. Polygon’s design flexibility is unmatched and includes; fiber winding, finishing, and more according to customers precise needs. The outstanding dielectric and insulating properties of Polygon’s industry-leading composite materials eliminate the risk of capacitance coupling, while their high torque strengths ensure durability.
Polygon Tube double insulation tubing holds an Underwriter’s Laboratories (UL) certification AFW-G-10. Polygon’s rigorous quality control standards ensure that every finished tube is tested at 5,000 volts minimum to guarantee its dielectric integrity.